Home » Differences between water washable and solvent washable flexo plates
Differences between water washable and solvent washable flexo plates
Flexo plates are essential for printing labels, flexible packaging, textiles, and corrugated cardboard. In recent years, water-wash plates have gained importance due to their sustainability and elimination of toxic solvents. However, the differences between water-wash flexo plates and traditional ones can be decisive in choosing the best technology for one’s application. In this article, we will examine the main differences between these two types of plates and analyze the advantages and disadvantages of each.
Flexo plates are an essential tool for printing labels, flexible packaging, corrugated cardboard, and textiles.
In recent years, the flexo printing industry has seen the introduction of new technologies and production processes. In particular, the introduction of water-wash flexo plates has revolutionized the way plates are produced and used.
But what are the differences between water-wash flexo plates and traditional ones?
Traditional flexo plates are made of photopolymer, a substance that hardens when exposed to light. The plate is exposed to a light source through a digital image or a negative, creating an engraved image on the plate. The plate is then washed with chemical solvents to remove the soft parts and leave only the engraved image. These plates have been used for many years and are still a popular choice for flexo printing.
Water washable plates on the other side use a production process completely different. Queste lastre sono fatte di polimeri termoplastici che si induriscono quando vengono esposti a una fonte di calore. Water-wash flexo plates, on the other hand, use a completely different production process. These plates are made of thermoplastic polymers that harden when exposed to heat.
Water washable plates are the right solution if:
- you want to produce at home without introducing solvents into the company. The introduction of solvents would require complex provisions for proper ventilation of the premises and frequent medical checks for operators.
- you require production speed for printing emergencies. Water-wash plates have much shorter production times than traditional plates, allowing clichés to be ready for printing within 20-30 minutes without waiting. Unlike solvent-wash plates, the cliché does not swell and therefore does not need to rest after the drying phase.
- you want to reduce the environmental impact of their production process since the use of chemical solvents is removed.
What are the advantages and disadvantages of these two types of flexo plates?
The main advantage of traditional solvent-based plates is the lower cost of the plate itself compared to water-developable plates. However, although the plates are cheaper, they hide higher management costs: in addition to the additional cost for the related development solvent, they require the management and disposal of the solvent, which has increasingly high charges.
The cost difference is overcome if we compare water-washable plates to new generation plates, also with solvent washing like NX plates.
Pure water-developable flexographic plates have Flat Top Dot technology without the need to purchase expensive equipment to create a flat-topped dot, and for this reason, they are already prepared for HD certifications in the digital version.
Until a few years ago, traditional solvent-developable plates were the only solution for those who print with water-based and solvent-based inks. From a quality point of view, traditional plates lasted longer. Water-washable plates of the old generation, also known as “hybrid” plates, were only suitable for UV inks. They were very simple to produce but were also less resistant.
Today, this is no longer the case: some water-developable flexographic plates like Aquaflex are compatible with any type of ink (water-based, solvent-based, or UV-based), are very resistant, and allow for numerous reprints.
Pure water-developable flexographic plates, on the other hand, are very environmentally friendly, as the use of chemical solvents is removed. The plates are biodegradable and only require a simple soap to be added to the development water.
In conclusion, the choice between water-developable and traditional flexo plates depends on production needs. It is undeniable that more and more companies prefer to avoid the use of harmful solvents and opt for more sustainable productions for the environment and their operators, especially in light of the speed and quality advantages guaranteed by water-washable flexo plates.
Do you want to try the quality of a water washable plate? Ask for your Aquaflex processed sample !
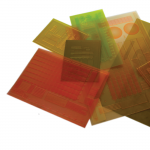